Automated electric multidirectional forklifts
The Phoenix from HUBTEX now available as an AGV
Concept creation
Manufacturing & integration
Commissioning & service
HUBTEX automated guided vehicles (AGVs) based on our electric multidirectional sideloaders provide innovative solutions for the efficient movements of long loads. Our AGVs are ideally suited to applications such as the handling of long goods in multi-shift operations. Typical HUBTEX applications such as the handling of long goods using load carriers can often be easily automated, offering users considerable advantages. Popular areas of application include, for example, steel service centers or facilities handling profiles in long goods cassettes. Drawing on the latest technology and an accumulation of knowledge, HUBTEX offers reliable solutions for demanding logistical challenges. Your company can rely on HUBTEX for efficient and precise material transport.
Sophisticated AGV solutions
for efficient long goods handling and process optimization
Handling long goods is a particular challenge for AGVs and requires specific expertise. HUBTEX has purposefully focused on this area when further developing its AGVs. The challenges of handling long goods require systems for load detection and identification and calculating the impact on fine positioning. Especially in long goods handling, the configuration of protection fields and travel routes has a significant influence on the design of the vehicle. HUBTEX sees this as a key development area and relies on navigation, safety and energy management technologies that are successfully established on the market.
AGV concept creation for a smooth, automated material flow
The success of an AGV project is determined by the AGV concept creation. The focus here is on individually tailored vehicle design and the precise selection of the latest sensors and control systems. We have extensively studied the concept of using the HUBTEX electric multidirectional sideloader as an AGV in a long goods warehouse and its integration into logistics processes. The vehicle is individually designed to ensure optimal performance and flexibility. Through comprehensive feasibility studies, we ensure that the investment generates long-term efficiency gains. We use simulations to optimize routes and workflows to achieve maximum productivity. Our concept guarantees a smooth, automated material flow in the long goods warehouse, increases efficiency and minimizes costs.
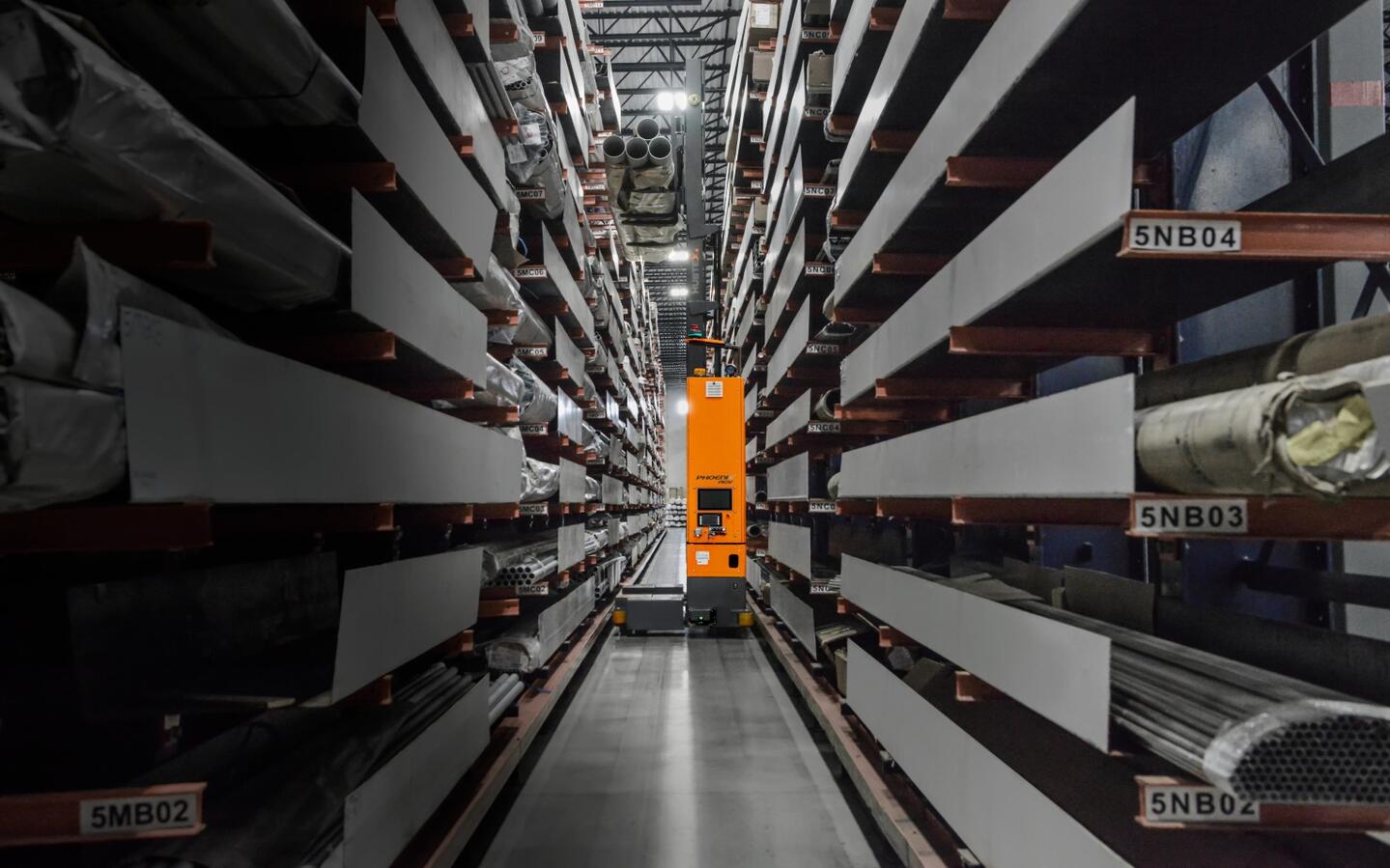
Process optimization
for enhanced safety and productivity
Throughout the AGV project, we will also advise you on ways to optimize your processes. The integration of AGVs should always advance operational processes by increasing efficiency, reducing errors and conserving resources. Typical benefits of using automated guided vehicles include the elimination of human errors, cost savings through continuous operation without breaks and flexible adaptation to fluctuating workloads. AGVs increase safety in the workplace because they navigate precisely and reliably. Time and route optimization minimizes waiting times and increases productivity. In addition, AGVs enable precise warehouse management by automatically tracking inventory and streamlining material flow. The use of AGVs makes logistics processes more effective, leading to improved overall performance and competitiveness.
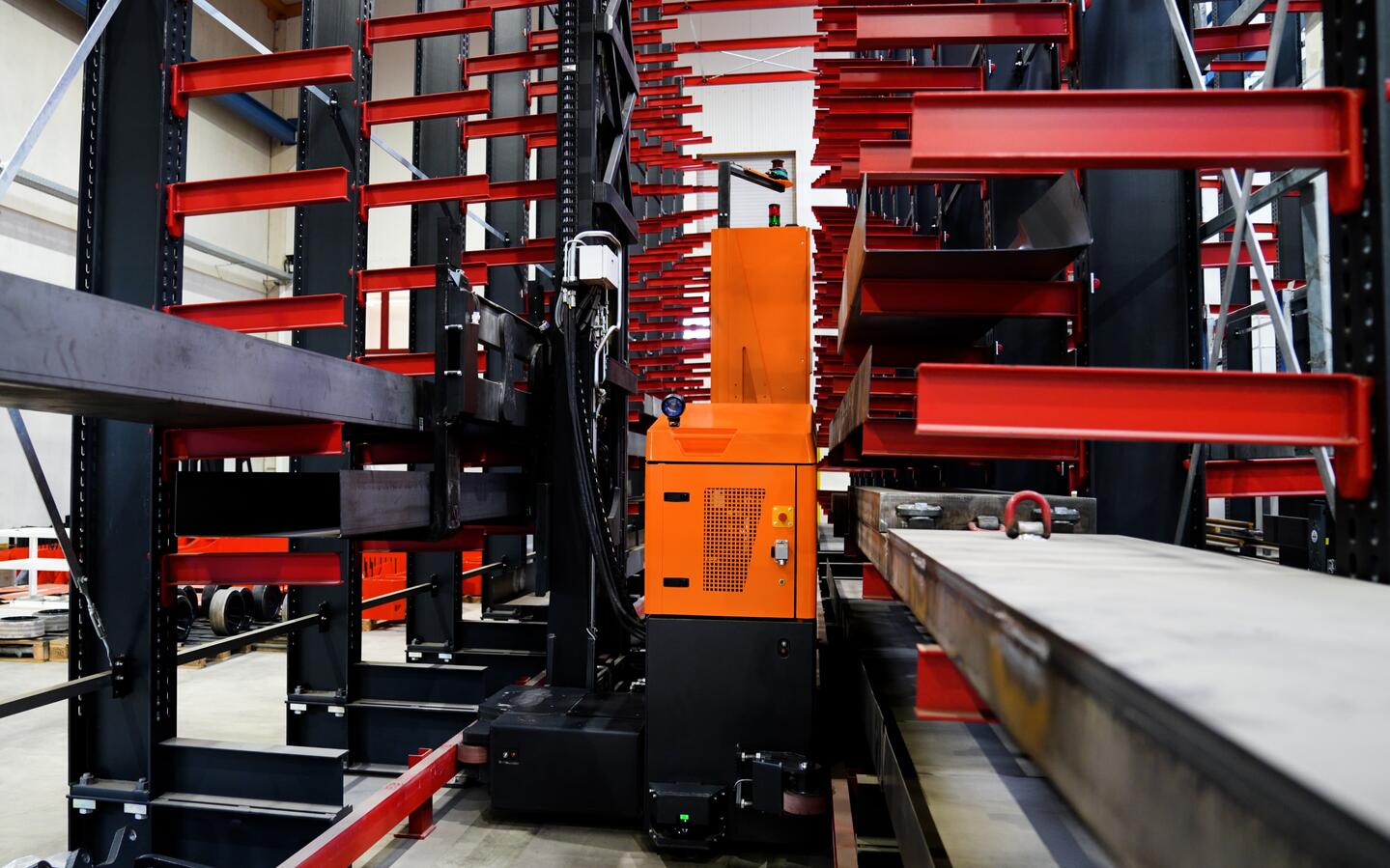
Great advice results in optimal solutions.
We know that handling long, heavy and bulky loads presents users with particular challenges. Arrange a no-obligation consultation appointment with one of our specialists to find the best possible solution for your application.
Features
Depending on the requirements of the application, route guidance and positioning accuracy, HUBTEX offers different navigation methods. These methods can be used individually, but can also be combined if necessary. The standard method for fully automated electric multidirectional sideloaders in typical applications is object-based laser navigation (also known as natural navigation). Laser navigation uses the data from a 270° laser scanner mounted at an elevated vehicle position to create a virtual map of the surroundings. In addition, the data from the personal protection system can also be used for navigation. The laser measurement, which is based on the structure of the building, is combined with the odometry of the vehicle. To optimize accuracy, passive reflectors can be installed in the warehouse.
When using AGVs, it is important that the vehicle always identifies the properties of the load. Once these properties are identified, routes, transfer situations and storage can be implemented reliably by the automated guided vehicles.
The safest way to do this is to use load carriers that are clearly defined in terms of length, width and height. If this is not possible, sensors are used as an alternative.
Typical areas of application for our sensors include load identification using barcode readers and load carrier detection using camera or laser sensors. Fork pocket detection for long goods pallets is also common.
We also have various technologies available to ensure optimal fleet management. If the higher-level WMS system already issues driving tasks, the range of functions of the existing navigation systems is often sufficient. However, if "order management" and "job prioritization" are not currently available, we offer our own fleet management solution developed within the group of companies.
AGV fleet management includes route optimization, battery management, coordination, maintenance planning, safety and emergency measures. The aim is to use the HUBTEX AGVs efficiently, reduce costs and increase safety. The primary functions include:
- Fleet monitoring: The AGVs are monitored by a central control unit that records data on location, operating status, battery charge level and error messages. This allows the performance and efficiency of the fleet to be continuously monitored and improved.
- Route optimization: Fleet management uses intelligent algorithms to calculate the best routes for the AGVs based on factors such as distance, traffic conditions and priorities of the driving tasks. This ensures optimal use of the vehicles and a reduction in empty runs.
- Battery management: Since AGVs are electrically powered, battery management is crucial. Fleet management monitors battery charge levels and schedules battery charging or replacement to ensure vehicles are ready for use.
- AGV coordination: In some scenarios, multiple AGVs must work together to complete complex tasks. Fleet management synchronizes AGV activities to avoid collisions and efficiently manage material flow.
- Maintenance planning: Regular maintenance of AGVs is crucial to ensure smooth operation and long life. Fleet management plans and coordinates maintenance work to minimize downtime.
- Safety and emergency management: Fleet management implements safety protocols and emergency plans to manage potential hazardous situations, such as malfunctions, obstructions, or unexpected events.
The safety of AGVs is of crucial importance to us. Our automated guided vehicles ensure safety by using laser scanners to protect people and machines, collision prevention and emergency stop systems. The scanners are fitted with a warning field to reduce speed and a protective field to stop the vehicle. Automatic restart can take place without acknowledgement.
In addition, certain areas can be defined as "safe" or "unsafe" using safety zones. To define safety zones, we install additional safety technology at the entry areas to these zones. This gives us the option of allowing vehicles to drive at higher speeds within these zones. These concepts allow us to control the access of people and to create clear boundaries.
Choosing the right charging concept for an AGV is crucial. Often, the different concepts have a significant impact on the degree of automation, acquisition and operating costs. A precisely tailored energy concept has an impact on the number of AGVs required and thus directly on the overall costs.
Generally, we recommend the use of lithium-ion batteries and charging AGVs via high-performance charging contacts. The AGV positions itself exactly above the charging contact, which is usually attached to the vehicle floor, and establishes the contact. As a contactless charging option, we also offer an inductive battery charging station. For large fleets, we offer automatic battery changing stations.
The emergency operation of AGVs is crucial to ensure that the vehicles can continue to operate even under unforeseen circumstances such as malfunctions or emergencies. We offer various solutions:
As standard, all HUBTEX AGV multidirectional forklifts can be operated manually by remote control in emergency mode or service mode. Many customers would like to be able to control the AGVs manually even with a cabin for emergency operation or in rare cases where human intervention is required. This vehicle specification is, of course, possible in principle. However, the requirements are examined specifically in each project.
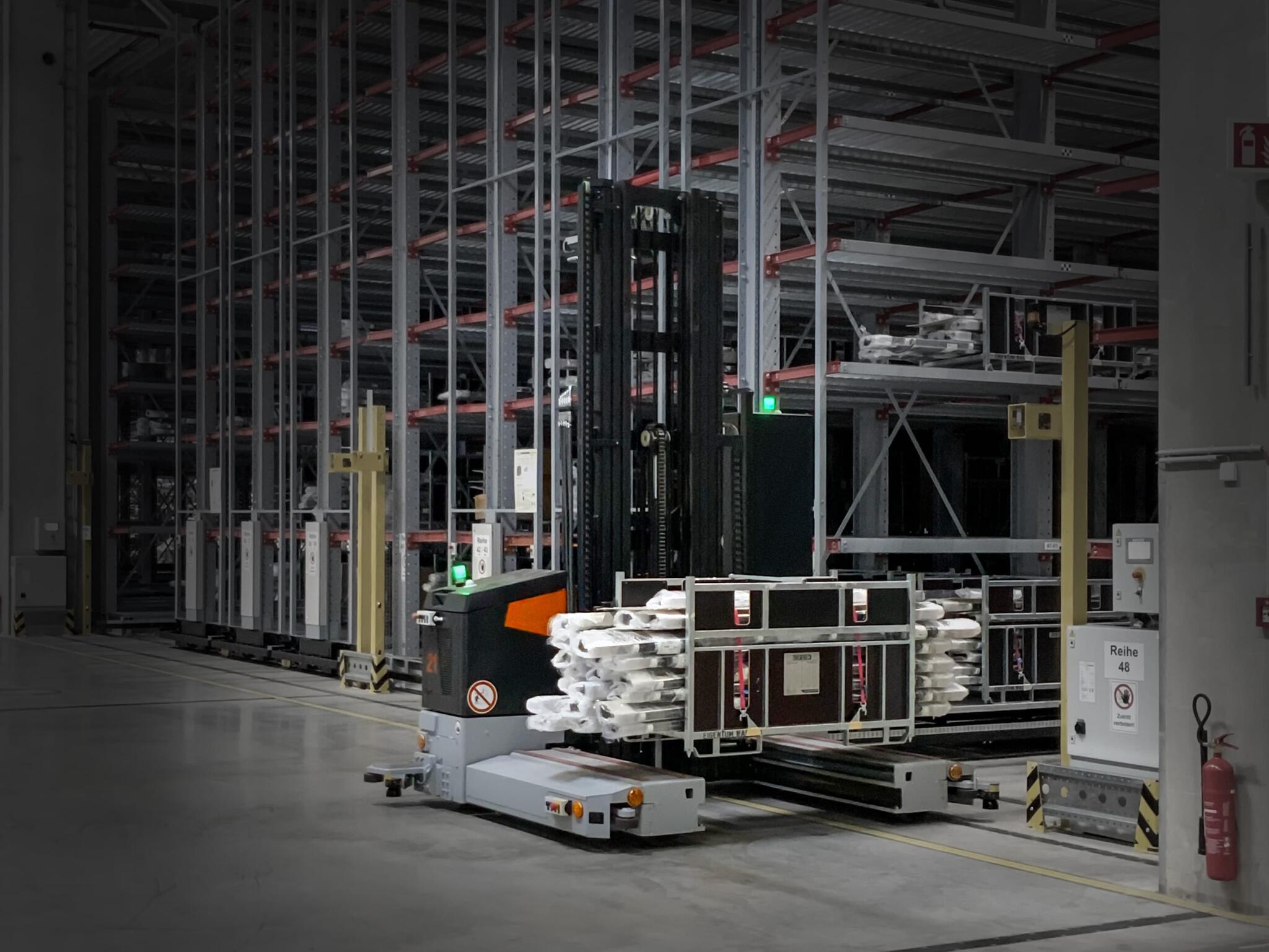
System integrators
for seamless integration and tailored automation
HUBTEX not only relies on its own AGV solutions, but also purposely maintains a partnership with system integrators. This cooperation offers our customers significant advantages in a large number of applications, including the seamless integration of various types of truck into a fully automated overall system, access to specific automation knowledge and improved service options.
The intensive cooperation between HUBTEX and system integrators enables AGVs to be individually adapted to existing logistics processes. This customization is based on pre-coordinated interfaces and thus guarantees efficiency, flexibility and smooth automation of material transport in a wide range of application areas.
HUBTEX service
Individual maintenance concepts and reliable support
HUBTEX offers you long-term investment security thanks to high quality service. We create an individually tailored maintenance concept with a precisely calculable cost structure. At the same time, we continuously train our staff and equip our vehicles with remote access facilities as standard for better diagnosis and support. Thanks to our comprehensive factory support, we ensure we find solutions to problems as quickly as possible. By exclusively using original spare parts, your truck remains a HUBTEX. You are investing in quality and durability.
Technical specification
PHOENIX AGV
Load capacity up to 25.0 t
AGV-specific hardware
Navigation
Fleet management
WMS integration
Load carrier detection
Safety
Battery and charging concept