Electric side loader
forklift
with multidirectional capabilities
The handling of long loads presents users with particular challenges. The loads have different dimensions and have to be transported safely and securely along narrow aisles. This calls for flexible vehicle concepts that can be adapted to suit the application. This is where HUBTEX side loaders come in with its multidirectional lift trucks. Over the past 40 years, the core product has been developed in countless variants. Our multidirectional side loader forklift is ideal for universal handling in specialised industries and helps companies with their warehouse logistics. Among other things, the side loader lift truck can transport long goods, stacks of metal sheets, chipboard, tools, cable drums, rollers, oversized pallets, and round bars in narrow-aisle rack systems. All lift truck types are freely movable both indoors and outdoors.
The right industrial side loader forklift
for your work.
Our four different product groups offer the widest variety on the market.
AGV-ready
PPE
Inductive track guidance
Cab option
Mast reach damping
Battery options
Two-part articulated frame
Special accessories
Rack guidance
Customizable effective widths
Multi-shift operation > 600 h/year
Individually adaptable | up to 35 metric tons | Lift height up to 14,000 mm
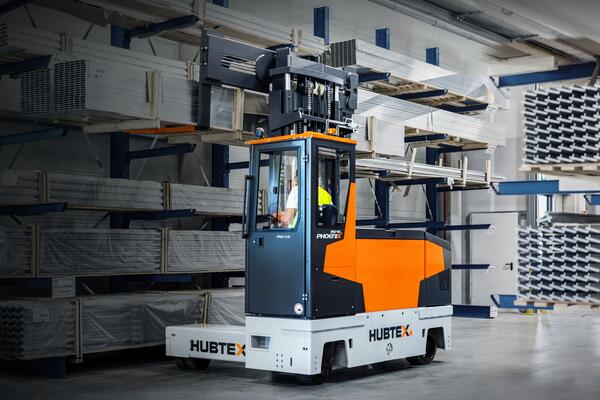
Mast reach damping
Batterieoption
Two-part articulated frame
Standard accessories
Rack guidance
Rack guidance
Standard effective width
Multi-shift operation > 600 h/year
The alternative to diesel and gas | Up to 4.5 metric tons | Up to 7.5 m lift height
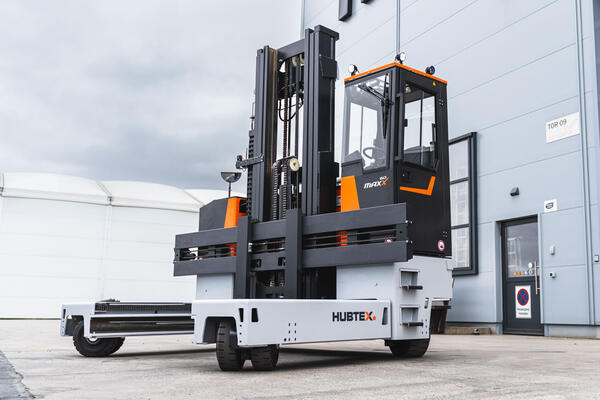
Single-part frame + three wheels
Standard accessories
Rack guidance
Standard effective width
Single-shift operation max. 600 h/year
Universal entry-level vehicle | Up to 3 metric tons | Three-wheel
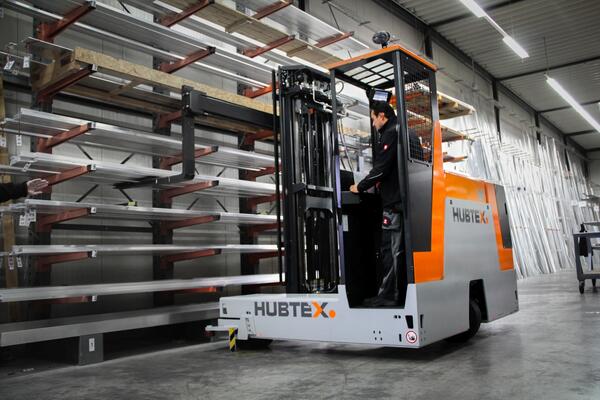
Single-part frame + four wheels
Standard accessories
Rack guidance
Standard effective width
Single-shift operation max. 600 h/year
Entry-level vehicle for indoor use | Up to 2 metric tons | Four-wheel
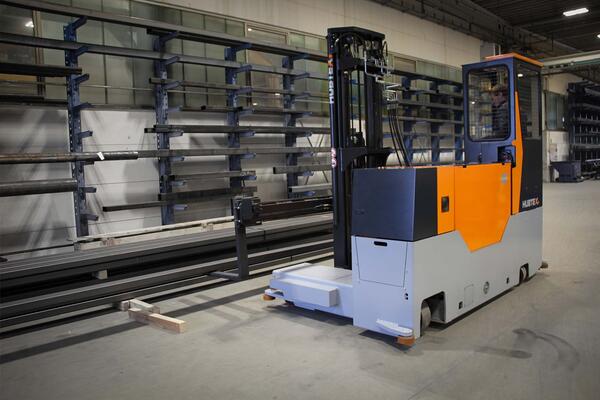
Discover the advantages for your application
We know that, when handling long items, users face particular challenges. To help us provide you with the best possible solution for your area of application, we recommend that you inform us of your individual requirements with just a few clicks
Optimising your workflows and processes in the warehouse,
thanks to our side loader lift trucks
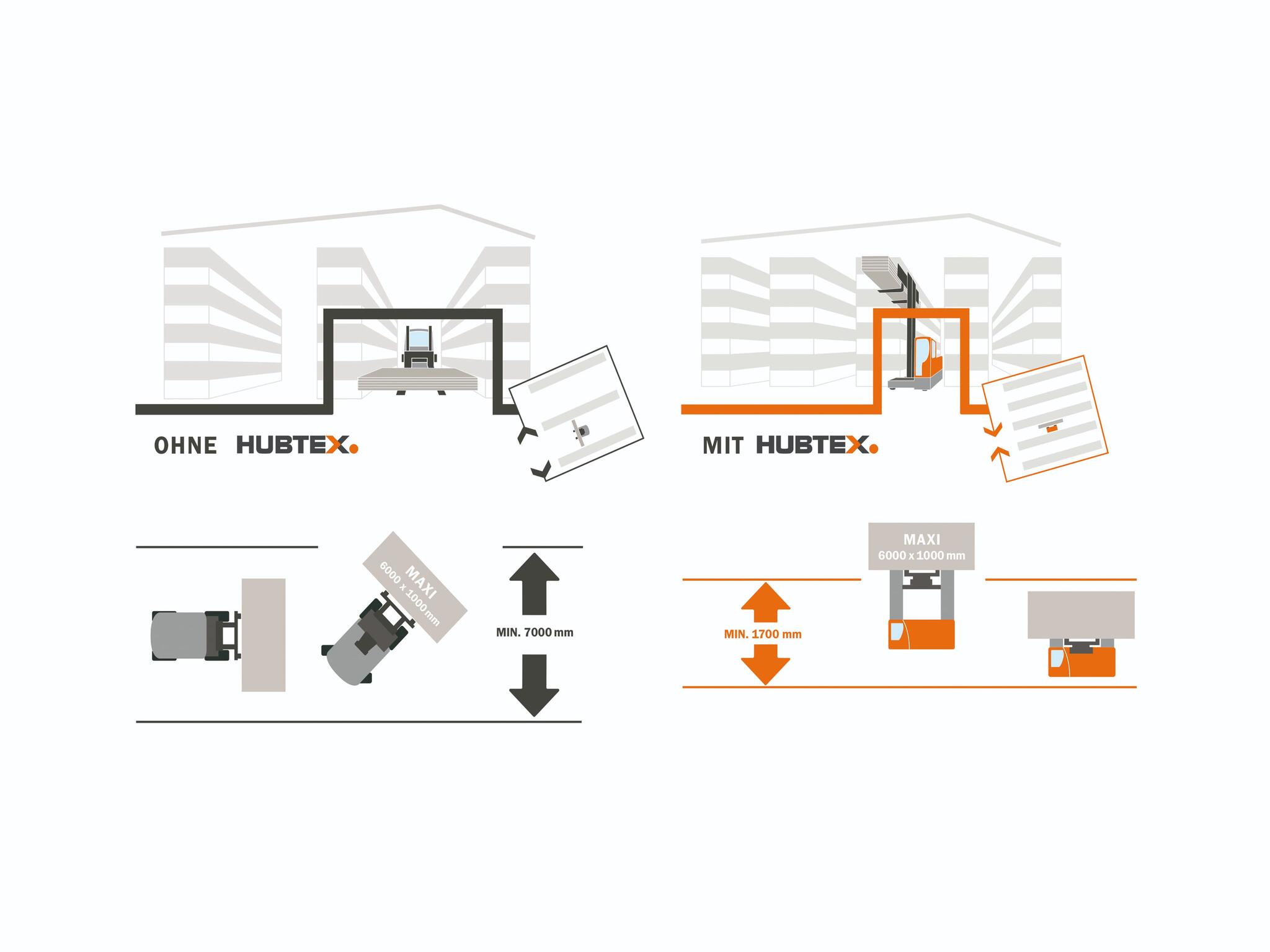
Making optimum use of warehouse capacity
Electrically operated multidirectional sideloader perform complex transportation tasks quickly, efficiently, and reliably. Using them to handle long goods allows narrow aisles to be passed through without any problems and the distance between rack rows and the widths of aisles are minimised. These benefits result in less damage to materials and vehicles, particularly where space is tight. Loads are brought safely, securely and accurately from the truck to their intended place in the rack thanks to a wide range of track guidance and operator protection systems. This creates space for additional rack rows and increased warehouse capacity. The forklifts impress with a smaller turning circle, more sensitive operation, and low noise.
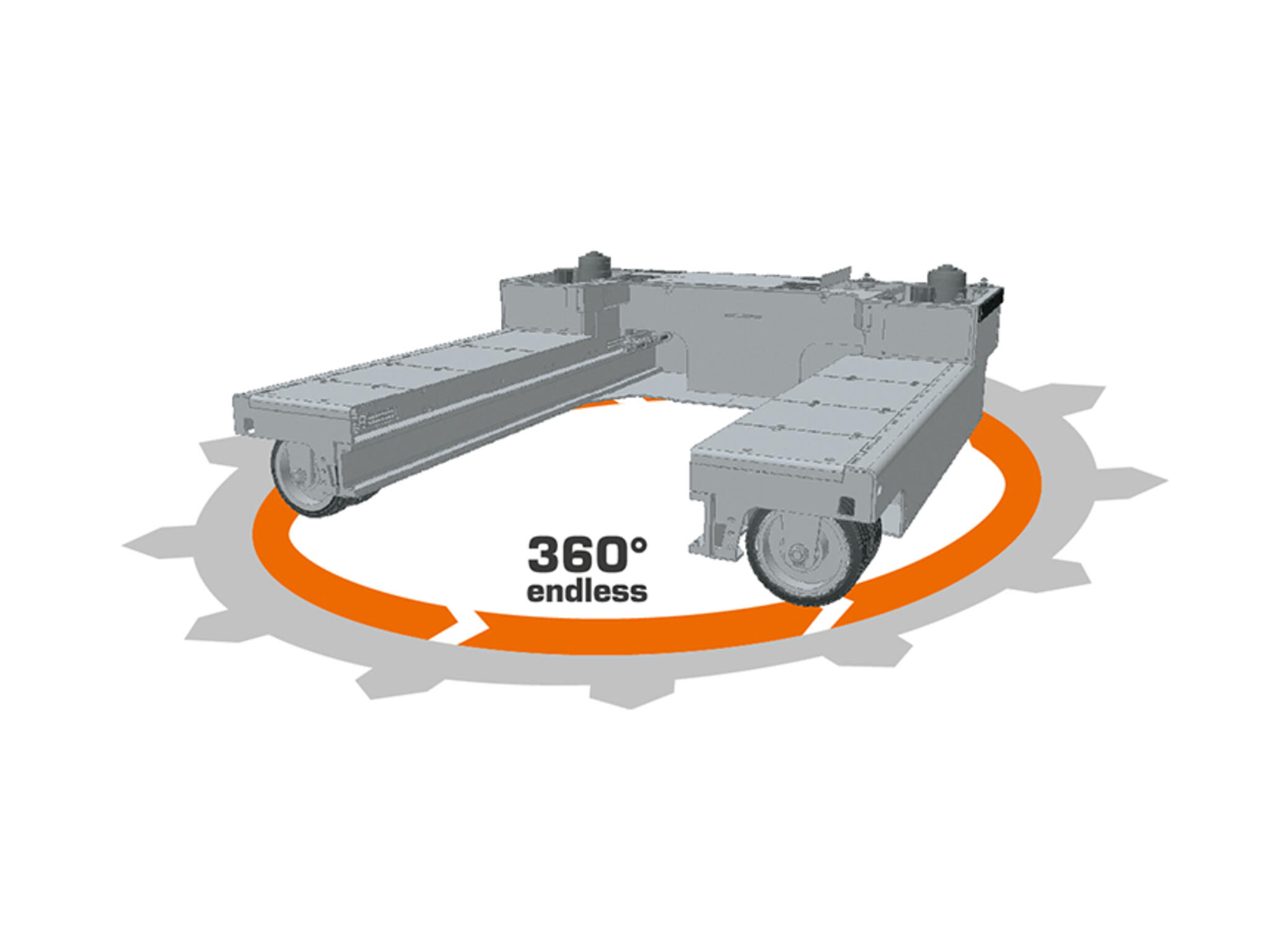
HUBTEX employs a range of steering systems: The patented HX multidirectional steering system is available for the PhoeniX and MaxX sideloader lift trucks, with 100% electric motor drives, being exclusive to the PhoeniX series. Although the two equipment features will ideally be combined, they also bring benefits when deployed individually. The HX multidirectional steering system enables HUBTEX side loader lift trucks to switch from longitudinal to transverse travel without stopping. This cuts the time needed to switch wheels and provides excellent manoeuvrability. A further benefit is significantly reduced wheel wear. As the vehicle changes direction whilst in motion, the wheels no longer turn on the spot. Typical areas of application include work involving frequent changes of direction in warehouses that allow ample freedom of movement, loading and unloading trucks, and block storage. Using an electric steering system enables energy consumption to be reduced by up to 85% compared with standard hydraulic steering. The electric steering motors only run when the driver actually steers. Electric steering systems are also virtually silent, making working much more pleasant for the driver. The lack of switching results in a tangible time gain. Nevertheless, HUBTEX still offers a hydraulic steering system, whose significant power reserves bring benefits if the multidirectional side lift truck is facing very poor floor/ground conditions and a high load capacity.
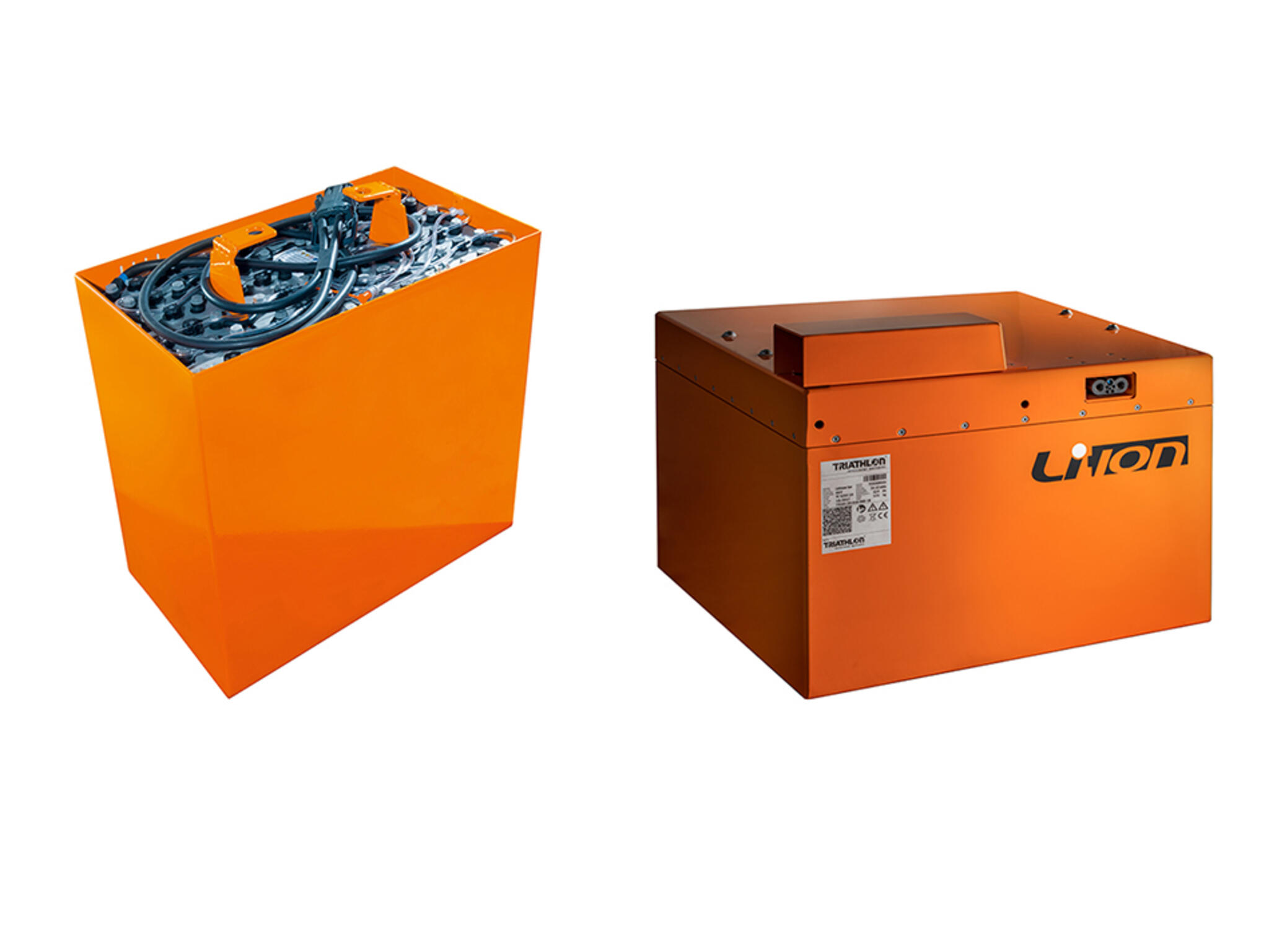
When you are purchasing a multidirectional side loader, we place special emphasis on the selection of the best battery system. A range of different types guarantees varying performance capacities depending on the area of application: Users with long operating times benefit from a fast return on investment through reduced charging and ancillary costs when using lithium-ion batteries. They are the logical choice for continuous two- to three-shift operation in which breaks can be used for intermediate charging. For applications with lower operating hours, the relatively low investment costs of lead-acid batteries make them the right alternative.
Charging concept customised for actual use
What’s the best combination of battery and charger for your application? Both 50 Hz chargers and high-frequency (HF) chargers are available. Their efficiency level will depend on the type of battery used. Whether the amount of energy you save will justify the extra cost of the better charging technology will ultimately depend on your operating hours. HUBTEX uses detailed comparative calculations to show you the most cost-effective solution. We compare the service life of the battery based on its price and usage to find you the most suitable combination of application and reliable technology.
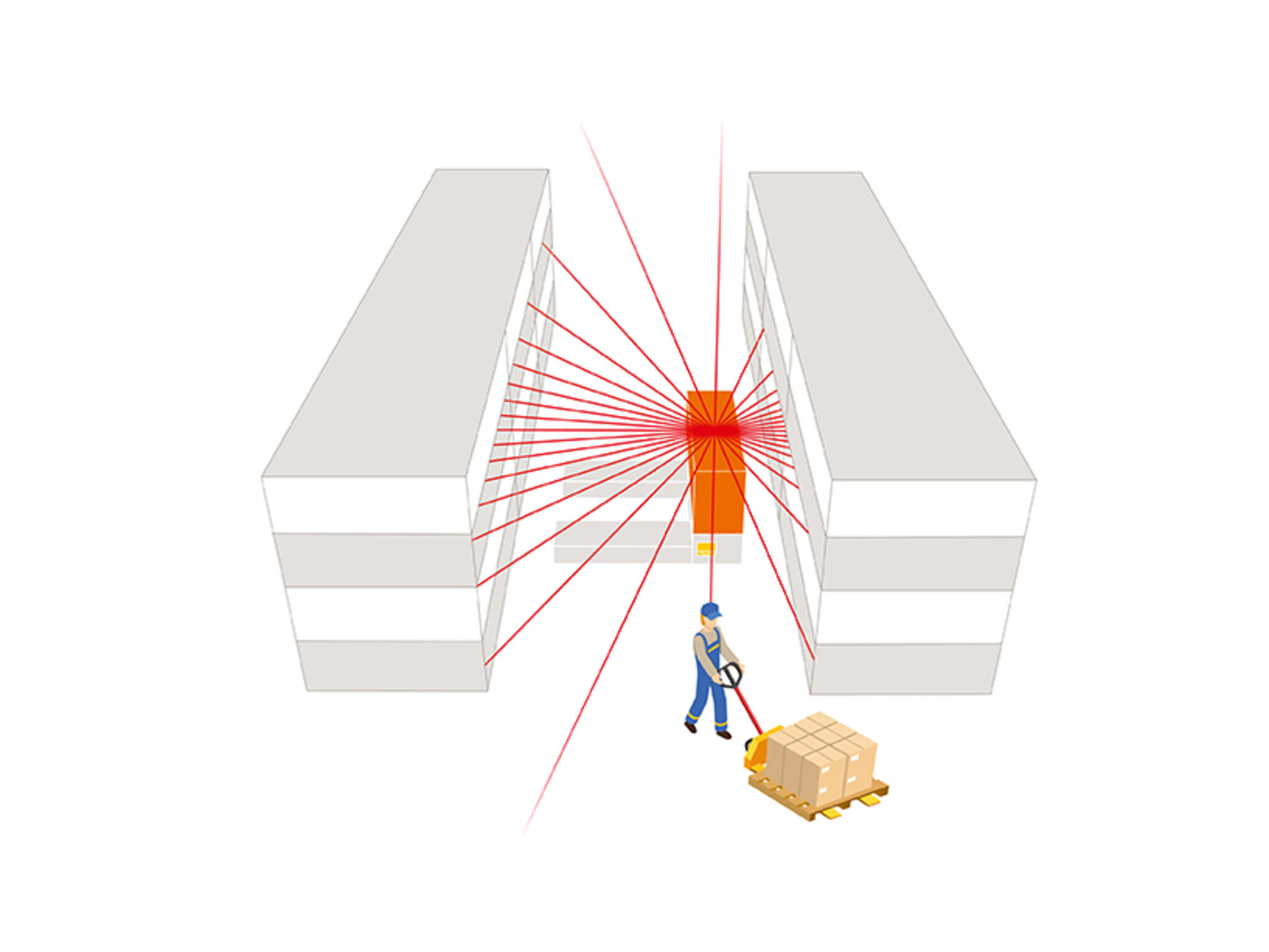
When you need to use picking equipment to handle long, bulky loads, HUBTEX follows the principle of bringing the operator to the goods. This reduces the work effort and prevents damage to the goods. To handle different requirements, HUBTEX provides polyurethane tires for smooth industrial floors, with the option of soft elastic tires for poor-quality surfaces or use outdoors. This protects the components and the health of the driver, as does a fork carrier tilt function for high residual load capacities and safe handling at high lift heights. Mobile operator protection systems are automatically activated when the rack aisle is entered and monitor it permanently using laser scanners. If the laser scanners detect persons or obstacles within the protection field in the aisle, the multidirectional lift truck will automatically be brought to a standstill. Powerful three-phase motors make the lift trucks really easy to drive on ramps and slopes and prevent them from rolling backward uncontrollably when they come to a stop.
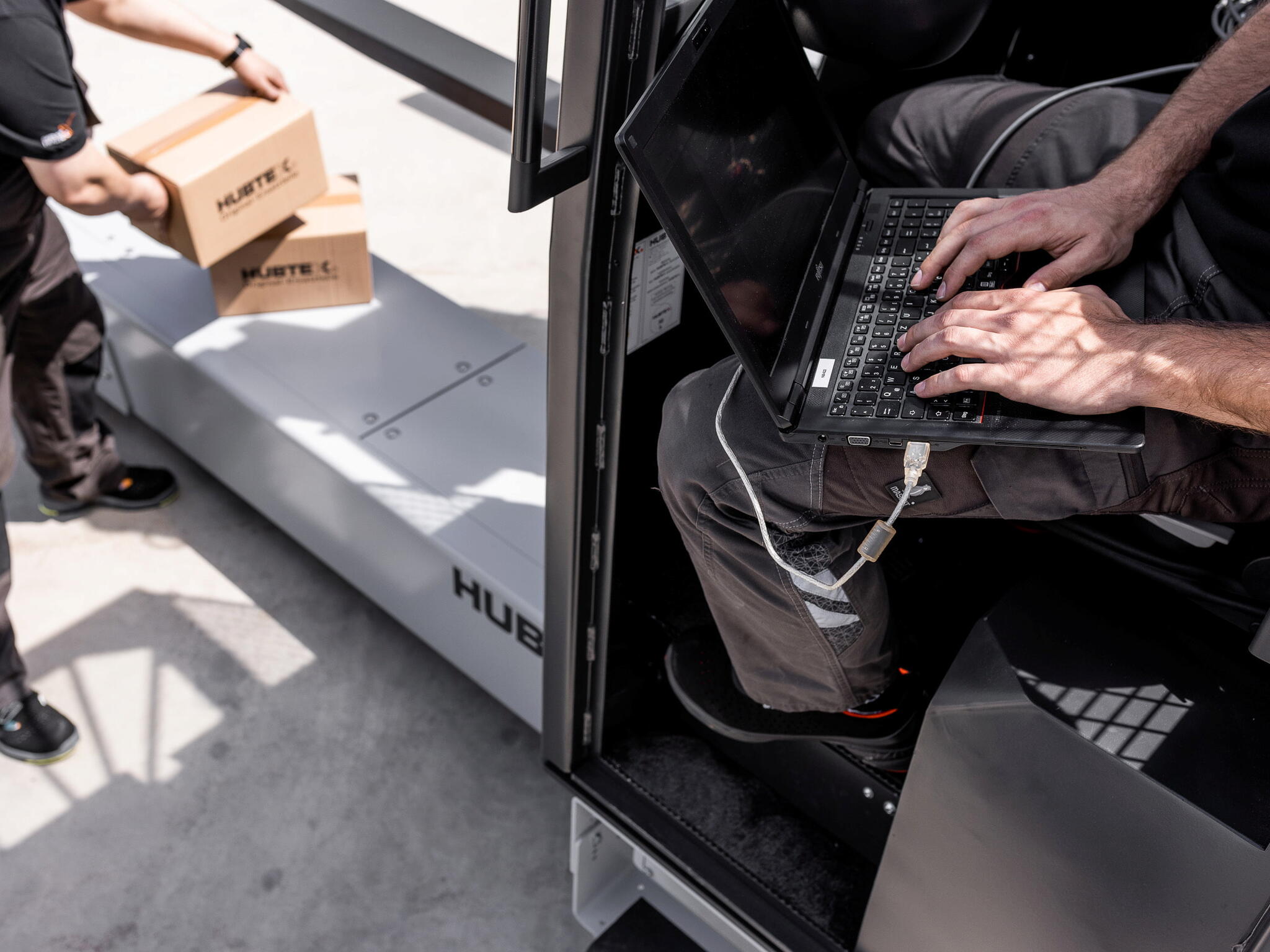
Series ESTL | PhoeniX electrical multidirectional lift trucks come with a remote maintenance system. This IoT solution transfers important vehicle data, such as fault codes and battery charge status, to a cloud, where it can be analyzed in real time. In the event of a lift truck malfunction, HUBTEX engineers access the vehicle’s data directly and provide fast assistance. The system detects the maintenance status of equipment automatically from its operating hours counter. HUBTEX can offer its customers preventive maintenance at just the right time. Users benefit from maximum machine availability, minimized production downtime, and predictive maintenance. Retrofitting on used vehicles is also possible.
We work together with you to assess your individual needs
HUBTEX will keep in close contact with you on all your projects and support you throughout the warehouse logistics process. We cover all the interfaces between production, warehouse management, automation, process digitalisation, efficiency planning, and energy management and combine them in the best possible way. Please don’t hesitate to get in touch.
Automated multidirectional lift trucks
A future-proof solution
Ever-growing requirements in the intralogistics business are making partially or fully automated warehouse processes increasingly important. HUBTEX proudly presents the world’s first fully automated electrical multidirectional sideloader for handling long, heavy, and bulky goods: The new PhoeniX electrical multidirectional sideloader modular system has been designed with gradual automation in mind, even in its basic configuration. The fully automated PhoeniX AGV has now been developed based on this core product. The vehicle is primarily suited to transporting long goods in the timber, metal, and plastics industries and is ideal for integrating into existing warehouse concepts. The vehicle’s basic features include dynamic mapping, precise positioning, and block storage. An object-based navigation system uses scanner data from operator and machine protection sensors to detect personnel and objects, while an interactive virtual warehouse map enables storage areas to be positioned and controlled. The position of the PhoeniX AGV inside the hall is calculated based on the scan results. At the same time, a load detection function allows long goods to be detected and picked up.
In each individual case, HUBTEX will assess whether full automation would make sense for the user and how much it would cost them.
Things worth knowing about the multidirectional side loader lift trucks
Answers to frequently asked questions
What is a multidirectional forklift?
The terms multidirectional forklift, multidirectional sideloader, four-way forklift, four-way sideloader as well as 4-way forklift are synonyms for the same group of vehicles. These vehicles are suitable for transporting long goods. For this purpose, you pick up the load from the side. The turning circle is considerably reduced by the multidirectional steering system.
When should a conventional sideloader be used?
2-way sideloaders are especially suitable for use in external warehouses for long goods. Their large tyres provide advantages on poor ground. This is described in detail on our special page.
Multidirectional sideloaders with electric or combustion engine?
In order to find the best truck for a particular application, it is not sufficient to consider individual aspects in isolation when selecting the right truck drive for a multi-directional truck. It is worthwhile for users to take a holistic view of the application areas, the total cost of ownership, the performance capacities and the service life. This is the only way to find the best individual solution. The development of electrically driven vehicles is rapid. Particularly in times of increasing environmental awareness of companies and the trend towards automation, it can be said that electric reusable forklifts are entering numerous new areas of application.
At Hubtex, we continue to focus on internal combustion engine vehicles, even though their share in our product portfolio has been steadily decreasing over the last few years and will continue to decrease. The areas of application for electric vehicles are expanding, but there are still application scenarios in which thermally powered industrial trucks are still clearly superior to electric vehicles. Accordingly, we are continuing to work on increasing the energy efficiency of our vehicles. One example of this is the development of our DQ-X model, in which we have placed energy consumption, noise minimization and ergonomics at the heart of the development of a diesel-powered four-way forklift.
Four-way sideloaders as well as 4-way trucks are synonyms for the same group of vehicles. These vehicles are suitable for transporting long goods. For this purpose, they pick up the load from the side. The turning circle is considerably reduced by the multidirectional steering system.
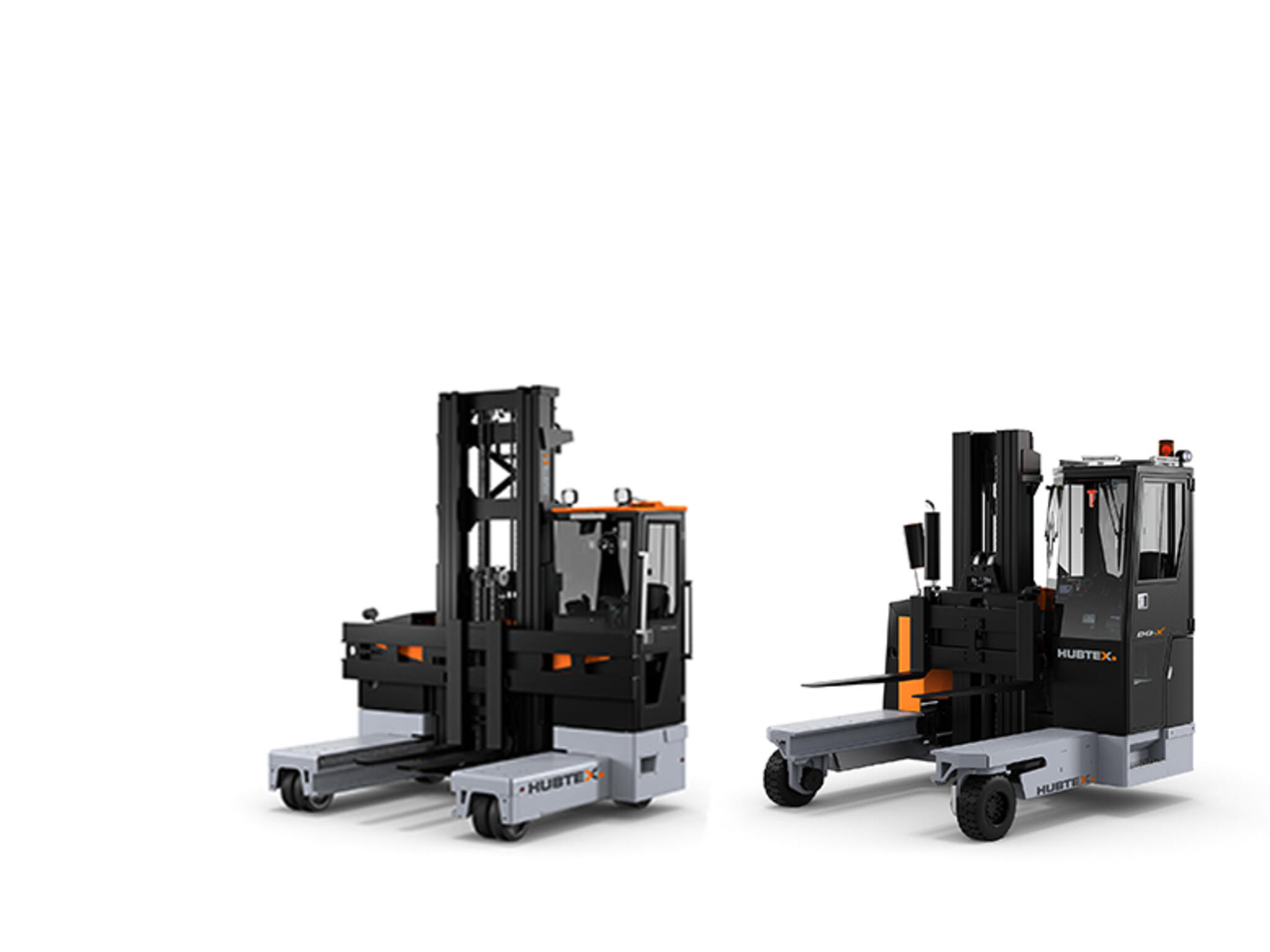
What is the difference between multi-directional sideloaders and four-way reach trucks?
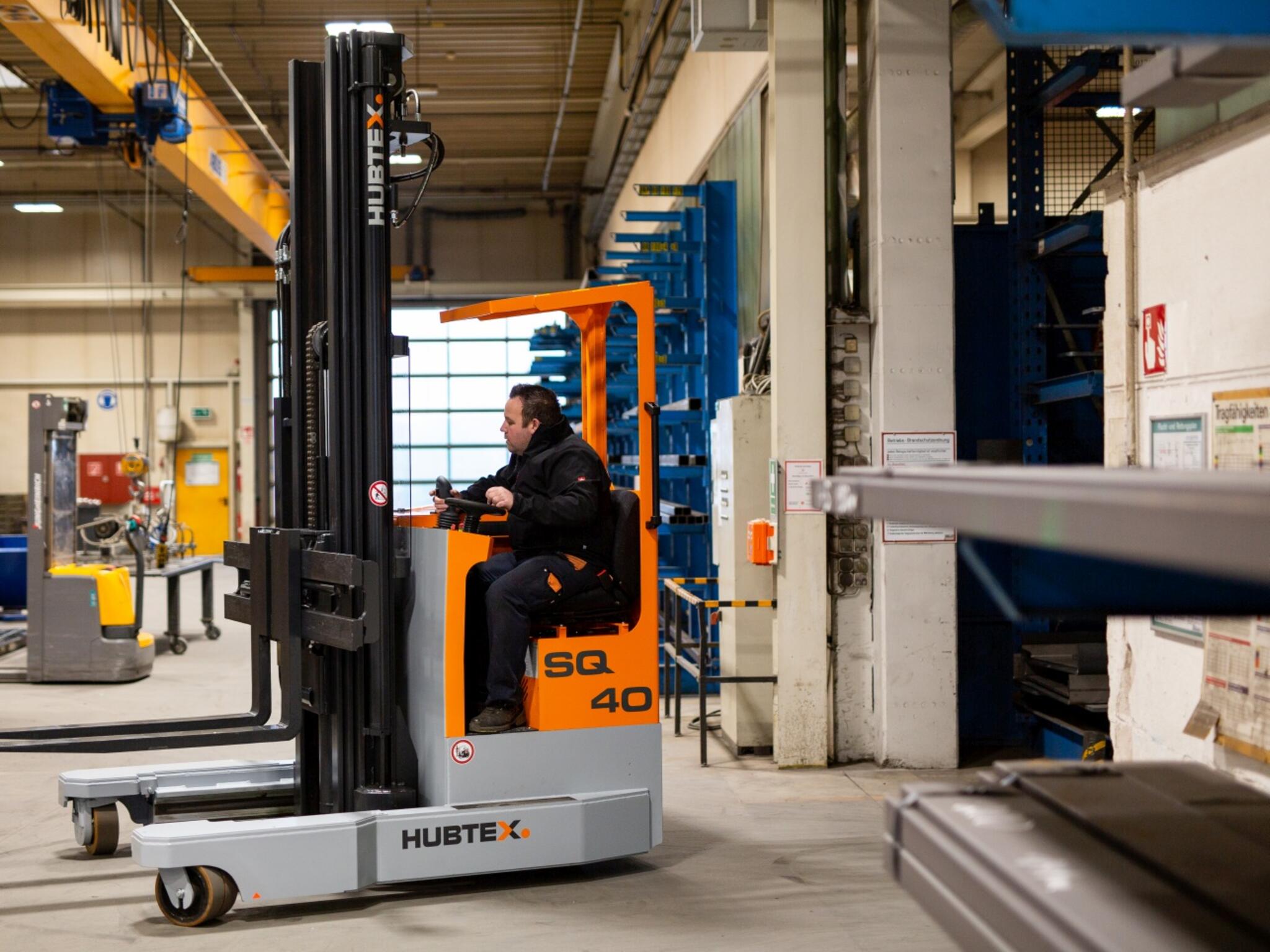
Both vehicle types are basically suitable for long goods transport. Depending on the area of application, however, there are differences between the vehicles due to their construction, function and dimensions. If there is sufficient space available to the user and/or the main part of all loads are Euro pallets and only rarely long goods and if only a hall application is planned, then a customer will certainly tend towards a four-way reach truck or a normal reach truck.
However, if the customer frequently has long goods loads and uneven floors made of asphalt or composite stone paving, then multidirectional sideloaders have clear advantages due to
- narrow width of the machine and therefore small turning radius,
- the load depth and load bed depth of the truck are identical
- the large mast feed = load depth + 100 mm,
- the 4-wheel chassis in a wide and stable frame and therefore better stability,
- the possibility of rail guidance,
- the two-part pendulum chassis to compensate for uneven ground,
- the vibration-damped driver's cab,
- the electronic 4-wheel steering system with 8 steering programs for precise movements,
- the two drive wheels and two double load wheels
- the larger wheel dimensions
- alternatively a soft elastic tyre for use on asphalt,
- the good view of the load or forks,
- of the identical length of the long fork carriage with the frame length,
- Constant vehicle width despite long fork carriage
- smaller "b"/"l2" dimension than for reach trucks
Why does HUBTEX offer vehicles in the same load capacity classes as 48V or 80V versions?
HUBTEX always tries to adapt its vehicles ideally to the respective application requirements. For this reason HUBTEX offers vehicles with 48V as well as 80V voltage, especially in the load capacity classes 3.0 to 4.5 t. As a matter of principle, HUBTEX does not offer vehicles in the load capacity range from 1.5 to 3 tons with a voltage of 80V. Here are some arguments:
PER 48 V (LOAD CAPACITY CLASS 1500 KG - 4500 KG):
- compact short design to allow small turning radii
- and to better enable block storage
- cheaper energy package in case of replacement procurement; also an important factor
- in the analysis of multi-shift operations
- lower weight of the vehicle, which leads to longer battery life
- and less wear on the wheels leads to
- Almost identical energy content with the same installation space
- Comparison of the energy content: 48 V x 930 Ah = 44.6 kW/hour |
- 80 V x 600 Ah = 48.0 kW/hour
- cheaper control components, cheaper spare parts
- for drive technology and working hydraulics
PER 80 V (LOAD CAPACITY CLASS 3000 KG - 10,000 KG):
- higher load capacities
- more performance due to larger pumps and motors
- slightly higher battery power
- Reduction of power losses, as less heat is generated by higher tension
CONCLUSION:
HUBTEX offers both 48V and 80V devices. Each HUBTEX device is designed in such a way that the relationship between required power, load capacity, battery capacity and voltage is optimally matched. For example, we can offer the customer an MQ 30 (2125) with 48 V but also alternatively an MQ 30 (2130) with 80 V. The main price difference is the price of the energy package.
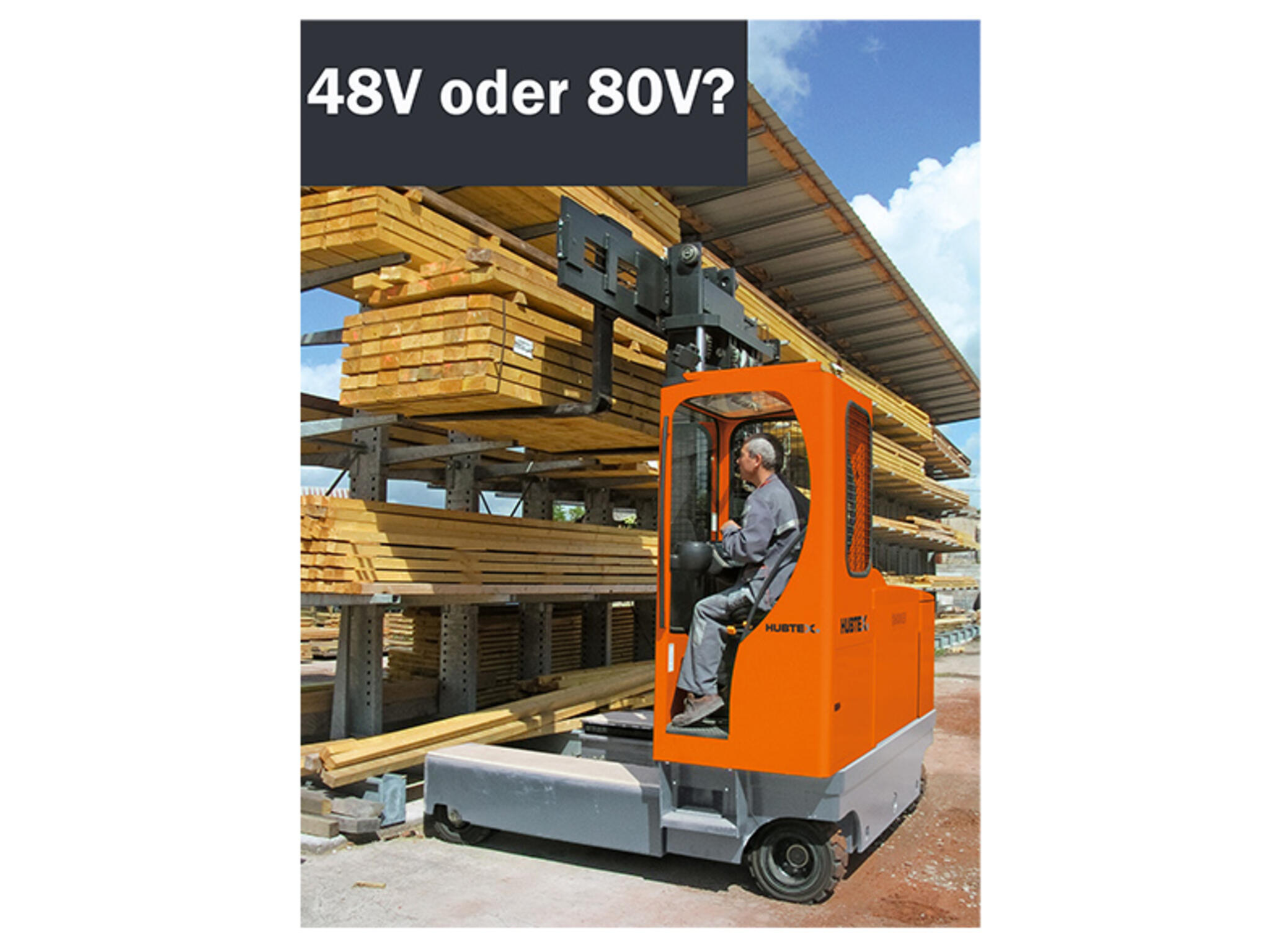
What is an HX multidirectional steering system?
By using the patented, optionally available steering system, it is possible to change from longitudinal to transverse travel without stopping. This reduces the time needed to change the wheels and offers optimum manoeuvrability. A further advantage is the significantly reduced wear of the wheels. As the change of direction takes place during travel, the wheels no longer rotate on the spot, which significantly reduces wheel wear and increases the service life of the wheels. Typical areas of application for the new steering system are applications with a particularly high number of changes of direction in freely movable warehouses, when loading and unloading trucks or in block storage.
What does HUBTEX call HIT?
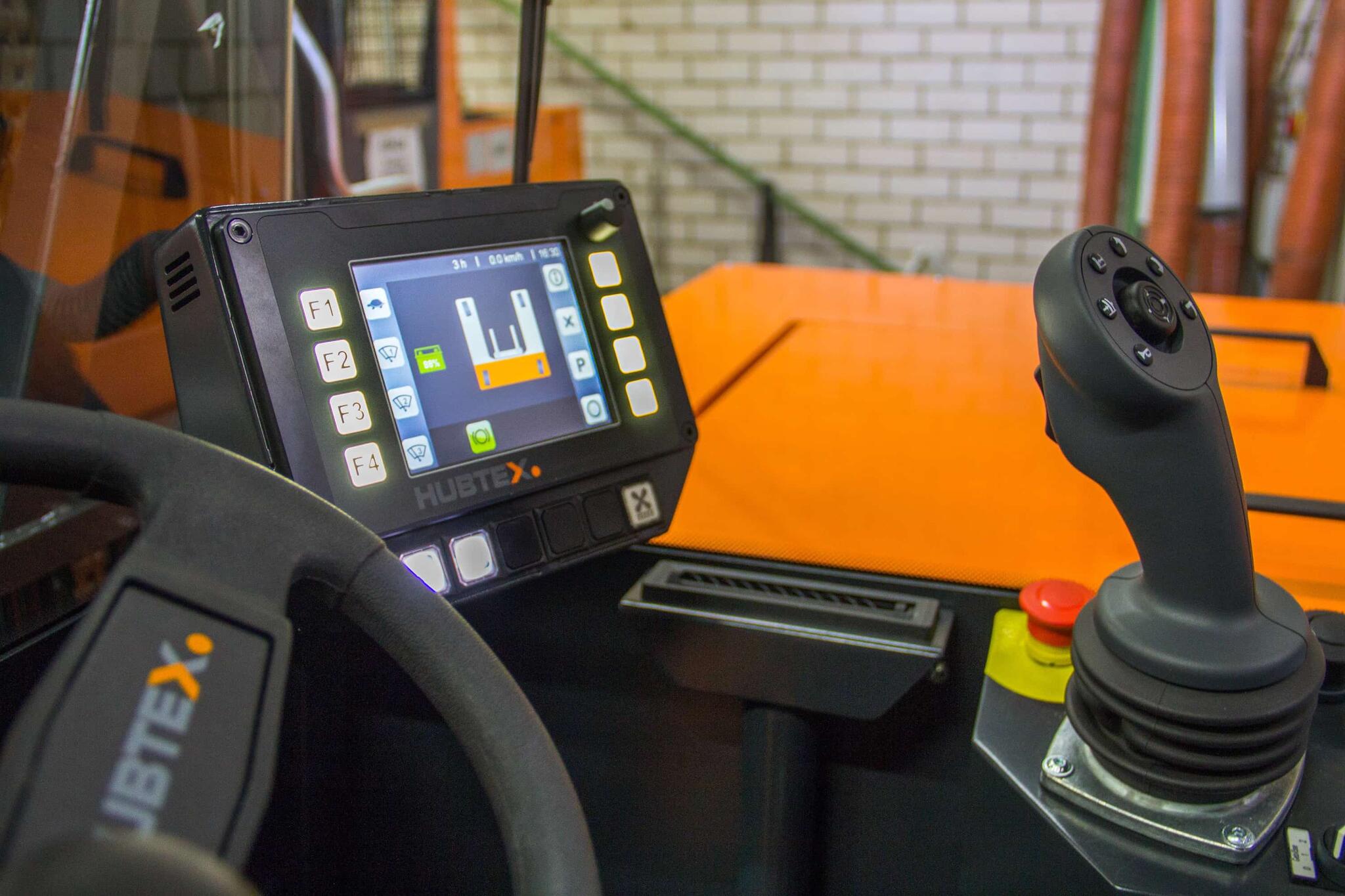
This is the information display for the driver in the cab. As a component of all electric multidirectional sideloaders, the FluX and MaxX models as well as many special vehicles from HUBTEX, the new HIT3 informs about all relevant operating conditions. The multifunctional display with its new visualisation provides the driver with all information on wheel position, speed and battery condition of the truck in a simple graphic display. Compared to its predecessor model, the new HUBTEX Information Terminal has numerous improved features. Depending on the customer's requirements, for example, truck access control can be carried out directly at the terminal with a personalised code. In this way companies can ensure that only authorised and trained employees drive the trucks.
Which accessories are available for HUBTEX vehicles?
HUBTEX vehicles are always adapted to the individual requirements of the application. This also includes the individual equipment of the vehicle with additional systems. The HUBTEX sales department has a comprehensive list of attachments, load handling attachments, storage aids, camera systems, load weighing equipment, steering systems, rack guiding systems, tyres, personal security systems as well as cabins and lighting equipment.

What is a narrow-aisle warehouse?
The narrow-aisle warehouse is characterised by its small footprint. The working aisle widths are accordingly kept as small as possible. In order to achieve a high degree of space utilisation and maximum storage capacity, the standard heights of the warehouse are also utilised to the maximum. The vehicles used travel with minimum safety distances and are guided in the aisle by track guidance systems. Furthermore, picking solutions can be easily integrated with the advantage that picking can be carried out directly in front of the pallet compartment. Other storage forms are the wide aisle warehouse or RGB or high-bay warehouse.
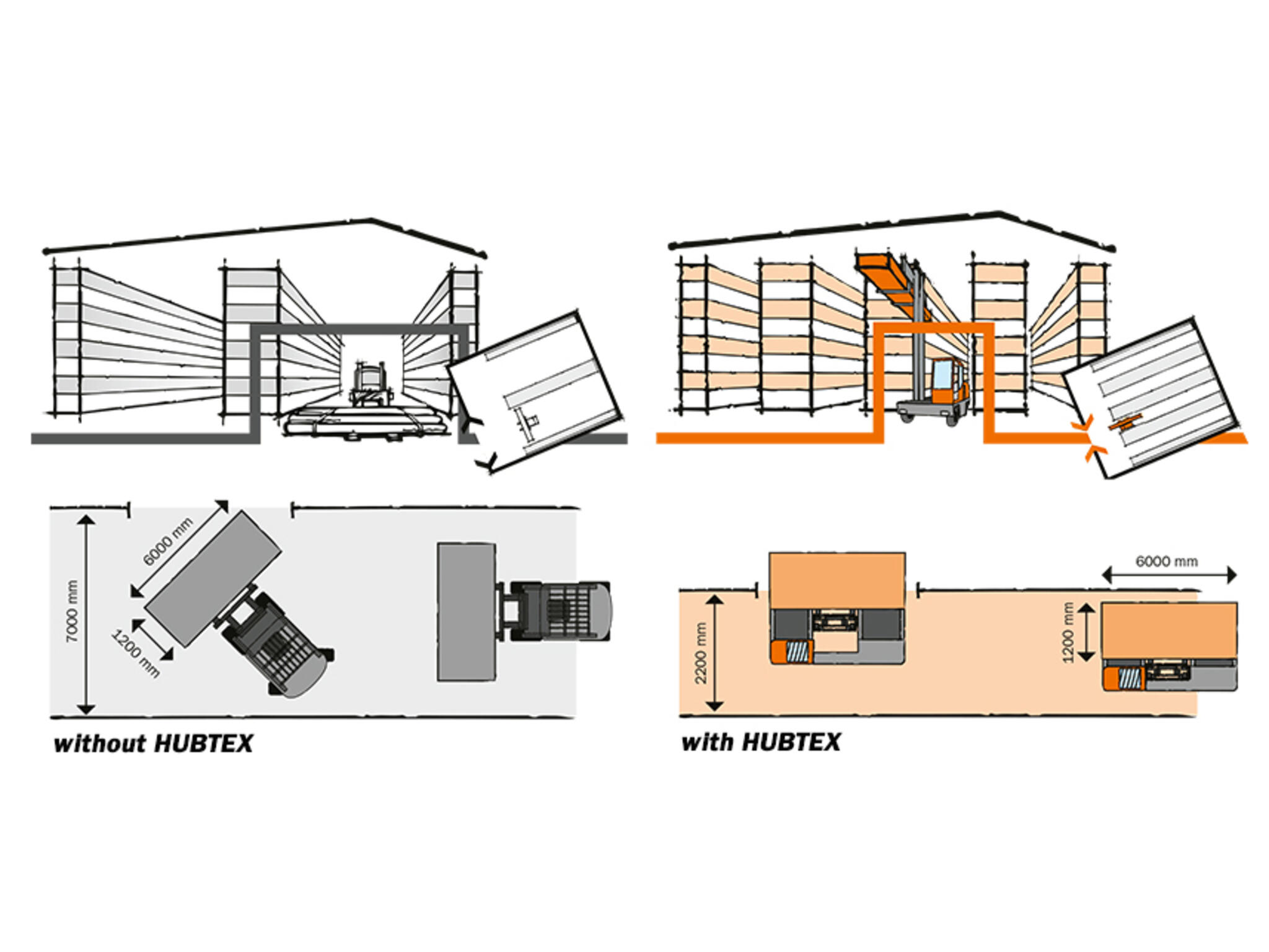
Which guide systems are available from HUBTEX?
In order to reduce the working aisle widths in a narrow aisle warehouse with minimum safety clearances, the installation of a guidance system is necessary to ensure high travel and lifting speeds and the necessary safety despite the narrow aisles. For maximum utilisation of the available storage space HUBTEX offers three different track guidance systems for narrow aisle solutions. With only 100 mm safety clearance per side the working aisle width is reduced to a minimum.
Here, the reusable stacker is guided by two guide rails fixed to the floor. The rollers, two on the left side and two on the right side, hold the truck in the rails in the middle of the aisle. The inclined entry angle, which can be detected, makes it easier for the driver to enter the lane.
The minimum width for the operation of mechanical guidance via guide rails results from three factors:
- the prescribed minimum safety clearances
- the stacking depth of the load
- and the individual truck configurations
In addition, the guide rails can be divided into high and low variants, whereby a minimum ground clearance of 15 mm is recommended for smooth operation.
Our experts will be pleased to support you in making the right choice for your guide rail system.
Here the forklift follows a stringline laid in the ground. This is fed by a frequency generator with a high-frequency alternating current (low voltage). This generates a concentric electromagnetic alternating field.
This field is detected by sensors mounted on the truck. This means that every change in the position of the truck is registered and an automatic compensating steering is triggered.
The truck is thus guided safely in the aisle.
Our experts will be pleased to help you choose the right guidance system.
The system is supported by the installation of transponders. These are embedded in the floor. As soon as the truck drives over a transponder, a specific function is activated on the truck. Examples of these functions are aisle detection, stopping the vehicle at the end of the aisle or reducing the speed before leaving the aisle.
The optical guidance system (150 mm safety distance per side) is based on the technology of inductive guidance and is used when the required iron-free space in the ground for the stringline is not available.
In the course of automation, Hubtex is also developing a laser-based guidance system.
Shelf guidance via laser localization
Laser navigation is a relatively new process at HUBTEX. The object-based laser navigation uses the raw data, e.g. the personal safety scanner or 2D laser scanner. The HUBTEX vehicle control system creates environment maps on the basis of the acquired data. The vehicle then identifies its own position within the map and is thus able to follow defined routes with an accuracy of up to +/- 15 mm. The procedure is tolerant of changes in the environment.
Automatic vehicle positioning
The horizontal and vertical vehicle positioning is an add-on for laser localization. As an alternative to laser localisation, automatic vehicle positioning can also be achieved by installing a barcode tape on the racking system.
The rack positioning consists of a horizontal and vertical positioning device as well as a touch panel in the cabin. After the shelf position has been manually entered into the HUBTEX touch panel, the shelf positioning is activated. By pressing the joystick for lifting and the accelerator pedal the shelf is approached semi-automatically.
WMS connection
The connection of the multi-directional forklift to the Warehouse Management System (WMS) is the next stage of expansion for automatic vehicle positioning and serves to connect the forklift to the WMS. The target height for storage/retrieval is transmitted directly from the WMS to the automatic vehicle positioning system. The driver only has to activate the lifting function. When lifting, the fork stops automatically at the correct height.
Which personal safety features (for drivers and for employees) are already built into your industrial trucks?
When planning a vehicle with our customers, the evaluation of the safety of the operators, the employees but also of the goods is an integral part of the standard procedure. We offer a whole range of safety systems for our vehicles. We distinguish between passive and active systems. Passive systems are, for example, distance warning sensors, optical and acoustic warning devices, ram and bounce protection devices. They are relatively inexpensive to install, but have the disadvantage that active driver intervention is still necessary in an emergency. For this reason, we offer active personal protection systems as another alternative, such as mobile and stationary personal protection systems, automatic aisle end guards, lift / drive cut-offs, speed reductions or warehouse navigation.
When should I use a personal protection system?
Narrow aisle racking aisles in warehouses are accident black spots in everyday operations. Traffic routes for power-driven or rail-bound industrial trucks must be wide enough that there is a safety clearance of at least 0.50 m on both sides of the traffic route between the outer limit of the industrial truck and the boundary of the traffic route. However, the safety clearances are often not feasible due to the system. For this reason, exceptions are possible if structural measures, access restrictions or protective installations on the industrial truck counteract the danger to pedestrians.
The safety devices differ between stationary and mobile systems. HUBTEX offers mobile systems for its vehicles.
- Alternative to mobile PPE
- automatic protective device
- Protection of persons when using industrial trucks in narrow aisles
- officially accepted
- Cost-effective alternative up to three shelf aisles
- Optional: Escape door monitoring / escape route monitoring
- Shelf aisle monitoring via two laser scanners
- If persons or obstacles are detected in the aisle, your HUBTEX automatically brakes to a standstill
- independent of the number of rack aisles
- two gait recognition systems